Application Characteristics
For non-invasive medical procedures, design aesthetics are almost as important as the results they promise to patients. The equipment must reflect a positive brand image while maintaining proper status indication. In many cases, the simpler a device looks on the outside, the more complicated it is on the inside. When a non-invasive medical device manufacturer wanted to upgrade its next-generation technology for a non-surgical machine and reached out to VCC, we met those needs and more with a custom solution.
Application Requirements
Initially, all the OEM wanted was a light pipe solution for a device that included an intricate, eight-piece logo to communicate treatment status. Each piece could illuminate on its own, or work together in unison with the other logo elements. In addition to maintaining the same pattern with the complicated client logo, design requirements included:
- Reusing the existing tooling for the illuminated logo on the front panel
- Attaining maximum brightness for visibility by medical staff and patient during treatment
- Delivering uniform illumination, even along complex edges of the logo elements
Solution / Approach
Our team decided to take a step back and look at the client’s design needs from a more holistic angle. We discovered we could not only provide the desired illumination and visual properties required but also optimize the existing design to save even more on production costs. Creating soft illumination throughout the intricate logo design required significant modeling to provide maximum brightness and uniformity along with a 150-degree viewing angle.
To test our concept, we provided a 3D prototype that was printed in our advanced design lab. Ultimately, VCC was able to create a more comprehensive solution that streamlined the client’s supply chain by providing a turnkey solution made up of:
- Light guide design, including simulations to determine how the light would perform
- Plastics manufacturing to produce the light guide
- PCB assembly
- Connecting internal components in house, including a backlit display, integrated card reader technology
Our team ran simulations to determine the ideal angles, placement, and composition of the LEDs and other illuminated components to achieve the desired visual properties.
Adding wire harnesses
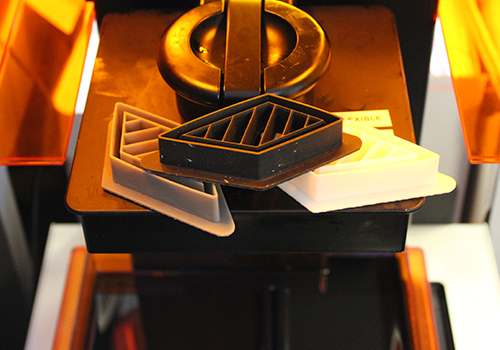
Result & Benefits
The VCC team exceeded our client’s indicator goals by developing a comprehensive solution to be used in new products as well as retrofitting existing devices.
- Faster development timeline thanks to VCC’s in-house 3D prototyping
- Fewer vendors and partners to manage throughout production
- Extensive quality and testing services under one roof
- Enhanced efficiency in production and manufacturing due to a simplified PCB design
- Significant cost and time savings
- Reduced risk of disruption or delays because manufacturing is taking place nearshore
Benefits to the end-user:
- Maximum visibility and reliability, even at 150 degrees
- Intuitive operation for treatment of non-surgical procedures
- Modern design aesthetic complements spa-like treatment environment
Value-Added Services
What could’ve been a simple LED order became a total solution where VCC helped the medical OEM reduce costs, complete more production steps at once and get their products into spas and medical centers even faster and more effectively.
In addition to providing the LED and illuminated components that were part of the original request, VCC offered:
- In-house 3D printing of complex prototype
- Integrated card-reader technology
- Custom light guide design
- Molded plastics
- PCB assembly
- Wire harnesses
- Quality assurance and inspections
- Testing
- Logistics
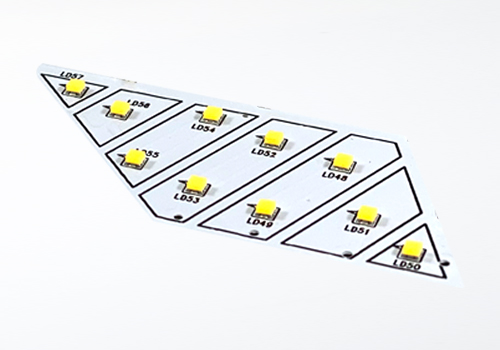
LED
We specified 152 1.18 mm x 1.18 mm LEDs and spaced them at precisely the right locations to attain 48.33% efficiency (compared to the industry average of a typical light pipe of 20%).
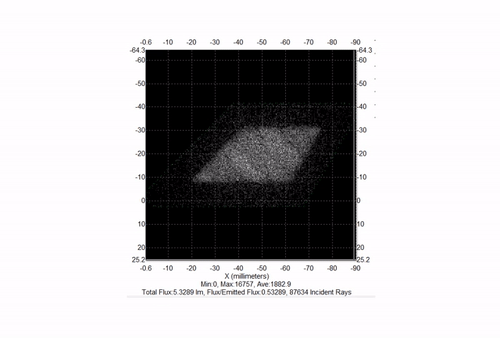
Light Guide
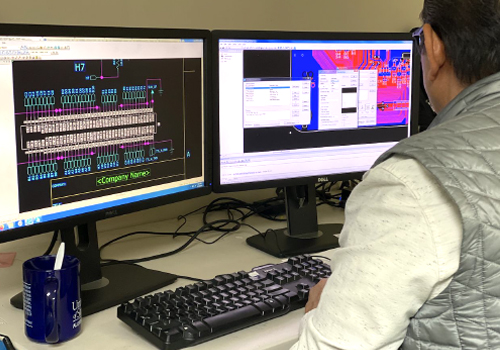
Custom PCB Assembly
The sophisticated design was streamlined by our team, who:
- Incorporated a metal core for heat dissipation
- Simplified the shape of the board, resulting in significant savings on materials
- Used a white solder mask to improve efficiency by 5% over the industry standard black overlay
- Added connectors, wire harnesses and other components to the back of the PC board, saving manufacturing steps and costs
Once assembled, this multi-layer solution includes the front logo panel, light guide in the same shape as the logo, and white metal PCB core with a simplified shape.
VCC took a simple component requirement and turned it into a comprehensive solution. Redesigning and manufacturing critical systems, our team reduced costs and TTM — while delivering a fresh, modern design!
VCC Solution
Industry Average
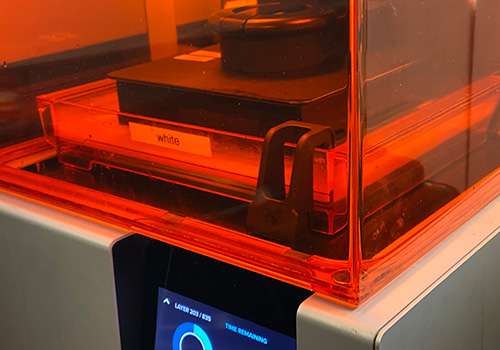
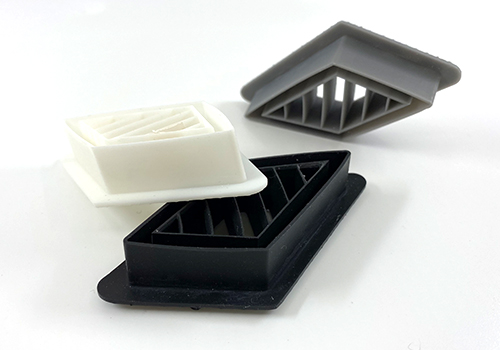
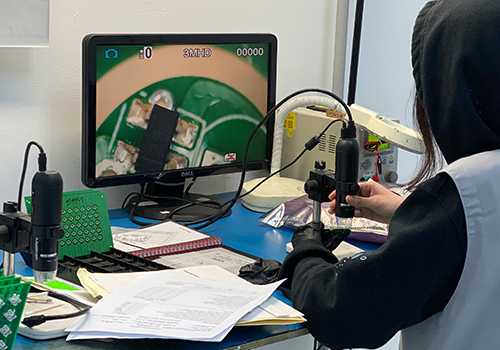
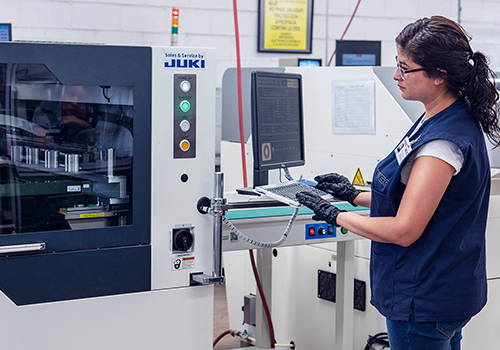
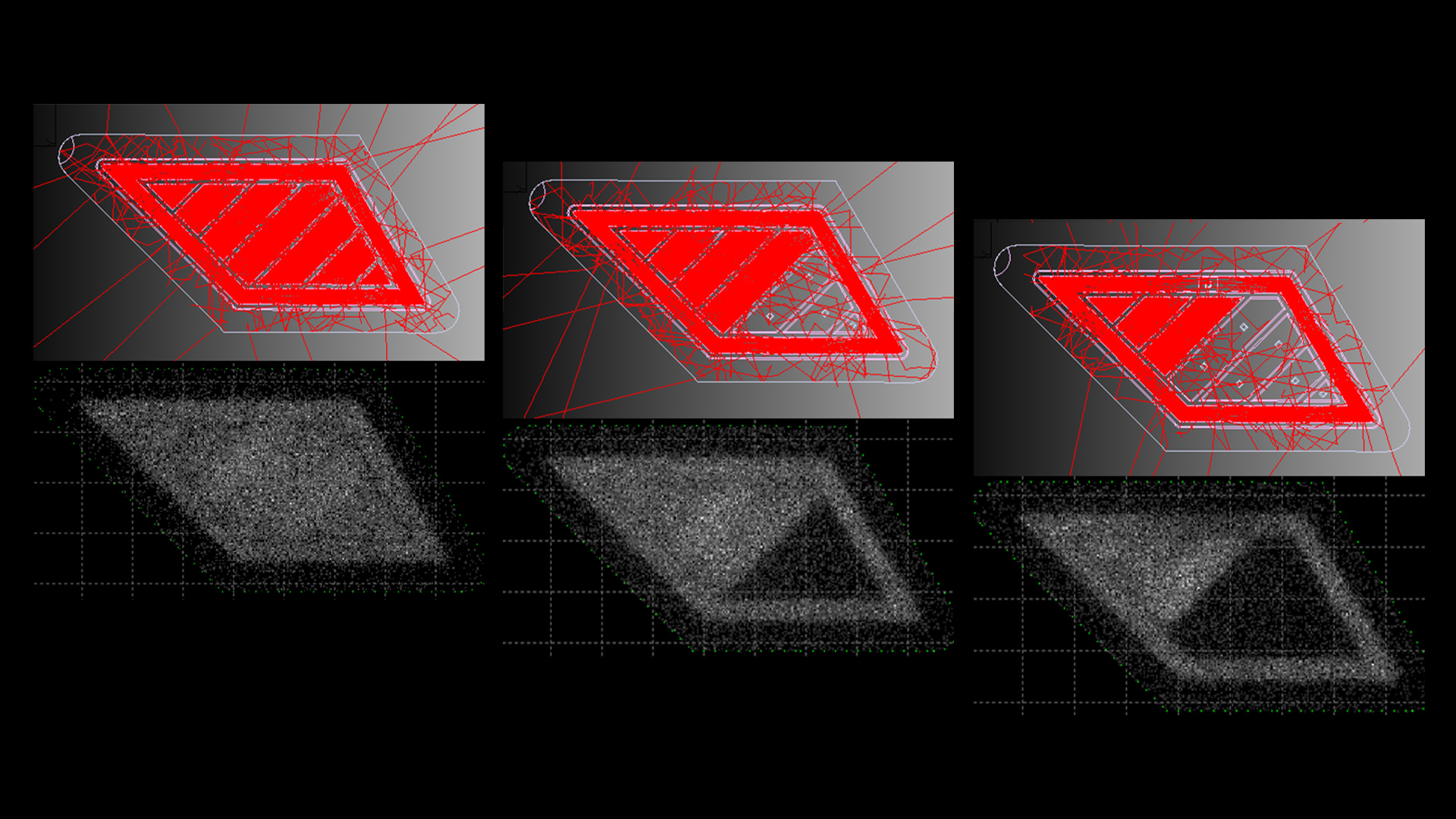
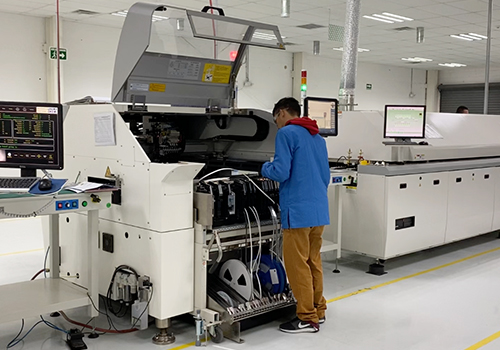