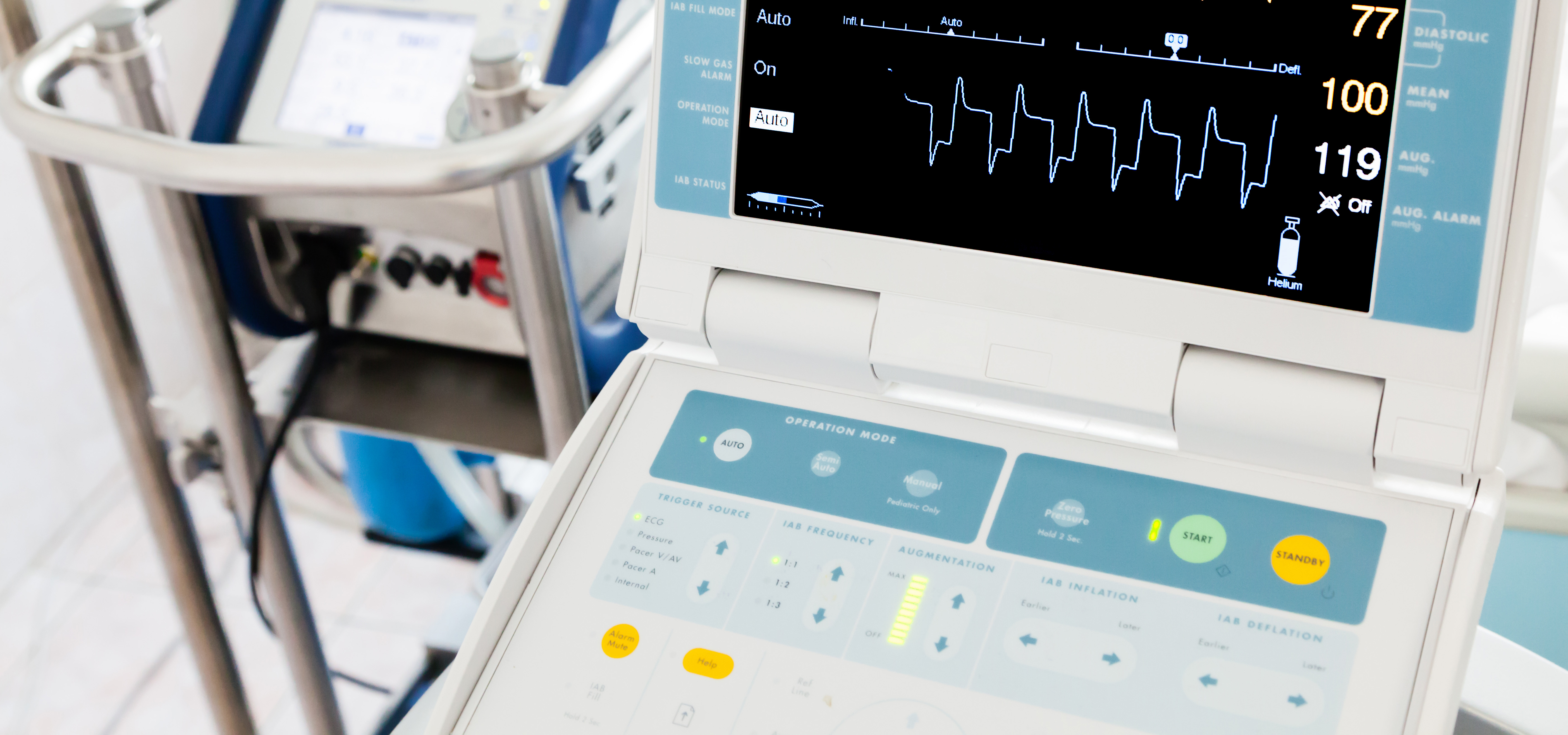
In the high-stakes world of medical technology, even milliseconds can make a life-saving difference. From infusion pumps and diagnostic analyzers to respiratory monitors, each human-machine interaction must be flawless. Membrane switches—though often hidden from sight—serve as the critical bridge between user intent and device response. These compact interfaces register commands with precision, endure rigorous sterilization routines, and maintain peak electrical performance over millions of actuations.
As quiet workhorses in a wide range of clinical devices, membrane switches enhance device reliability, simplify sanitation, and elevate user trust. A single failure can derail workflows, lead to compliance issues, or compromise patient safety. This makes their integration not just an engineering decision, but a clinical imperative.
Medical environments are among the harshest operating spaces for interface components. Devices must be intuitive, reliable, and robust against:
● Constant sanitization with caustic disinfectants
● Gloved or impaired touch (from PPE)
● Exposure to bodily fluids or lab chemicals
● Rapid user handovers between shifts
Mechanical buttons often fail these tests—succumbing to moisture ingress, feedback degradation, or intermittent contacts. Studies such as the ECRI Institute’s 2023 Top 10 Health Technology Hazards report attribute over 30% of infusion pump failures to UI errors, underscoring the human-factor risk inherent in device design
Built for the Front Lines: Anatomy and Advantages of Medical Membrane Switches
A membrane switch is a flexible, layered interface that closes or opens an electrical circuit when actuated. It typically includes:
● Graphic Overlay: Chemically resistant top surface (often polyester)
● Spacer Layer: Maintains separation to avoid false triggers
● Circuit Layers: Conductive tracks that close a circuit under pressure
● Backing Adhesive: Bonds the assembly to device housing securely
● Sealed to IP67: Blocks pathogens, fluids, and particulates—essential for infection control
● Low-Profile Ergonomics: Enables slim, easily cleaned devices with no debris traps
● Custom Tactility and Illumination: Responsive through gloves; optional LED backlighting ensures usability in dim environments
● Long Life Cycle: VCC assemblies regularly exceed one million actuations without performance drift
Compared to mechanical switches, membrane switches offer longer uptime, fewer service events, and reduced contamination risk.
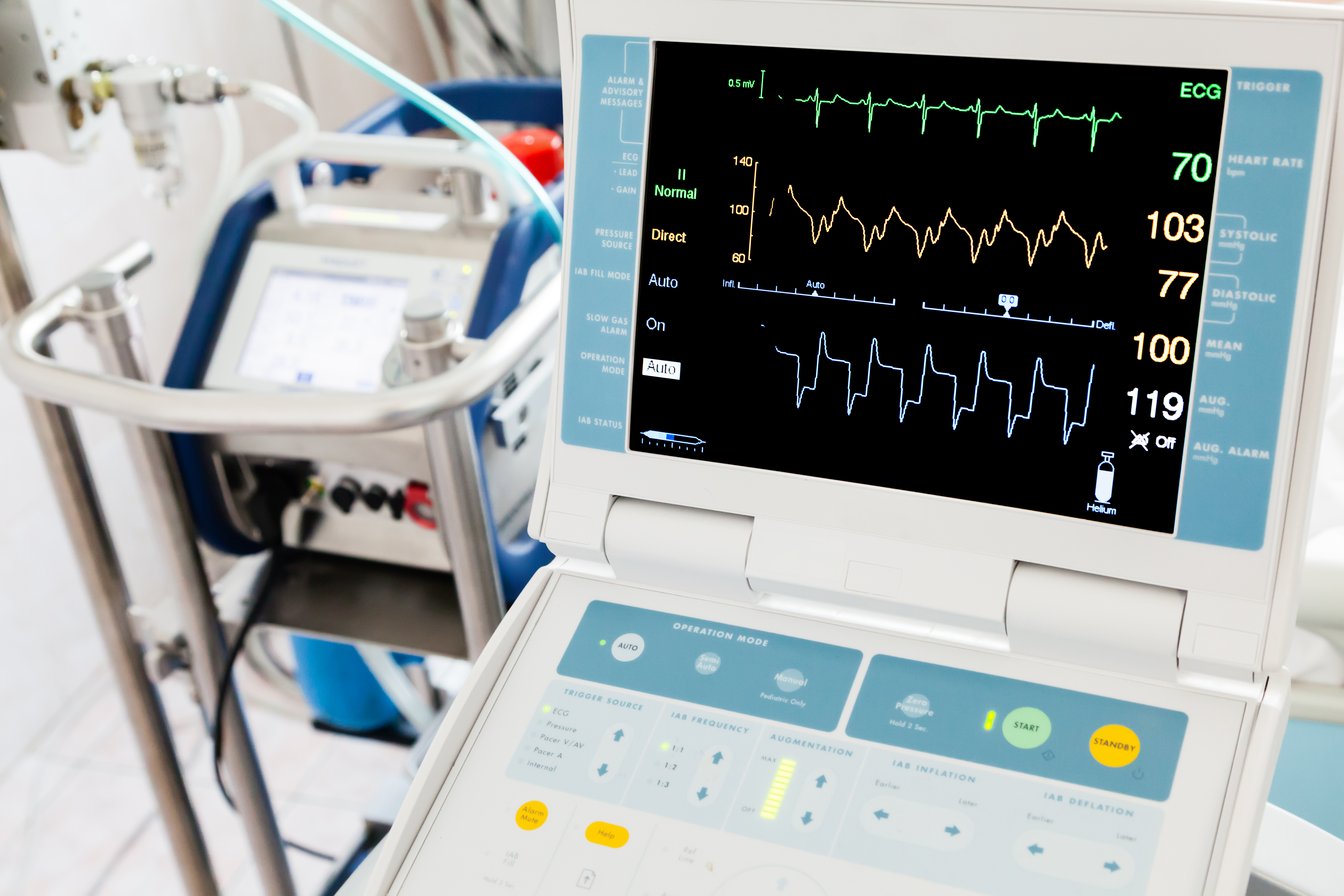
Tailored for Every Medical Setting
VCC collaborates with device engineers to customize interfaces for:
● Point-of-Care Devices: Large graphics, fluid-proof designs
● Lab Analyzers: Chemical-resistant layers for daily disinfection
● Home Care Equipment: ADA-compliant legends, anti-microbial coatings, integrated lighting
We blend human-centered design with production-grade reliability, minimizing design risk and maximizing user trust. Learn more here
Q1: Why choose membrane switches in infection-prone settings?
Membrane switches are fully sealed, wipe-clean, and withstand disinfectants—meeting IP66/67 standards.
Q2: Will they work with gloves or in low light?
Yes. We tune tactile response and offer LED backlighting for high visibility, glove-friendly operation.
Q3: Are they globally compliant?
Yes. VCC solutions meet FDA, ISO, IEC, and CE mark standards with batch traceability.
Q4: How do they compare to capacitive touchscreens?
Membrane switches provide tactile feedback and reliable actuation in moist, gloved, or high-static environments where capacitive switches often fail.
Q5: What customization options are available?
From tactile dome force to overlay printing and EMI shielding, VCC engineers build solutions aligned to exact medical use cases—rapidly and at scale.