Pizza Heater Cabinet
Industry
Foodservice
Retail
Hospitality
Technology
Expertise
Design Consulting
Design & Engineering Service
Multiple Lighting Technologies
Products/Services
1050 Series PMI
PCL22 Series PMI
High-voltage PMI
IP65-Rated Product
Standard Product
Nearshore Manufacturing
Application Characteristics
In the food industry, consumers have high expectations when it comes to flavor and consistency. One bad experience can result in not only the loss of a customer, but also a negative online review that could impact future sales.
And pizza heating cabinets are the perfect vehicle for providing a seamless self-serve experience — but only if the quality is there. Customers can order and pay online or through an app, then receive notification when their pie is ready. They can then go straight to the pizza heater to pick up their order — no line, no waiting, and no human interaction. The key to success in this self-service model is maintaining the highest levels of quality and freshness.
Food warmers like pizza heating cabinets must perform a few key functions:
Keep the food fresh, hot, and safe
Maintaining the right temperature and relative humidity required for freshness and food safety should be top priority
Maintain constant, real-time communication
With the pizza restaurant employee on one side, and the consumer on the other, both sides need to constantly illustrate operation status
Be simple to understand
Operation shouldn’t require any special training or instruction for employees or customers
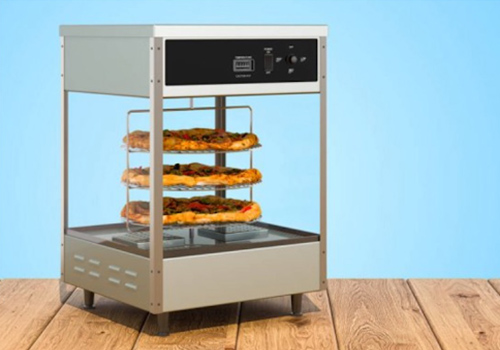
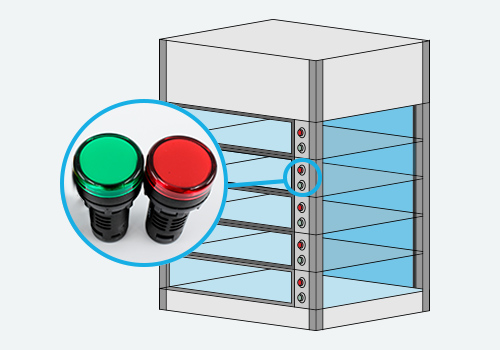
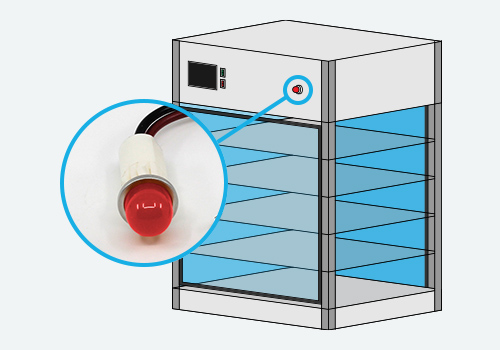
Application Requirements
When designing food equipment like warming cabinets, several considerations should be taken into account:
01. Cabinet height and placement
Must be designed in ways that are easily reachable and visible for consumers
02. Versatility
Which types of foods will need to be kept warm? What moisture conditions will need to be implemented?
03. Volume and dimensions
How many items will be heated/housed at once?
04. Control panel / user interface
The more intuitive the better for all users and customers
05. Accessibility
The heater should open from two sides — one for employees to place the pizza in from behind the counter, one for consumers to pick it up.
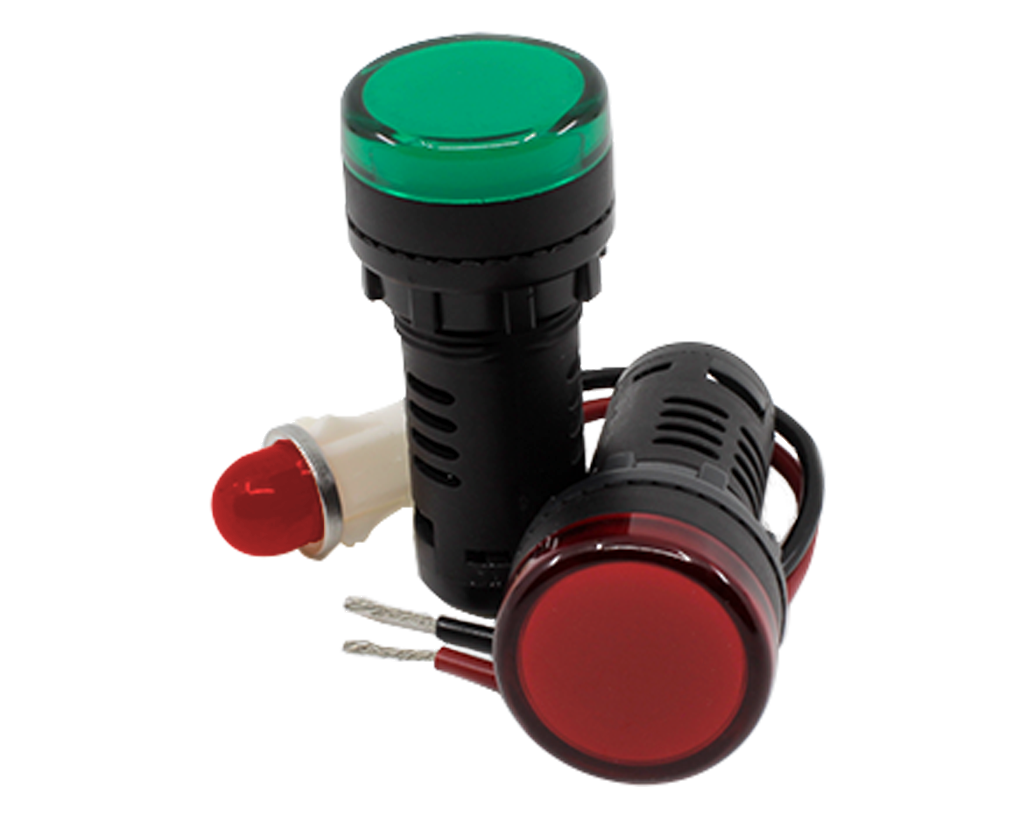
Caleb Hwang
Mechanical Engineer, VCC
Solution/Approach
1050 Series
The 1050 Series Neon Panel Mount Indicator with wire leads was used to provide bright, consistent illumination in 125V. This red neon indicator easily snaps into a 12.7mm hole and supports quick and easy assembly during production. Available in 125V or 250V, as well as a range of lens options.
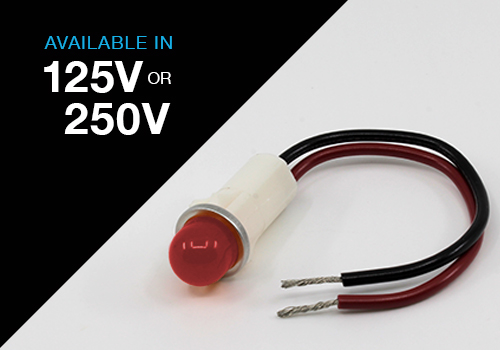
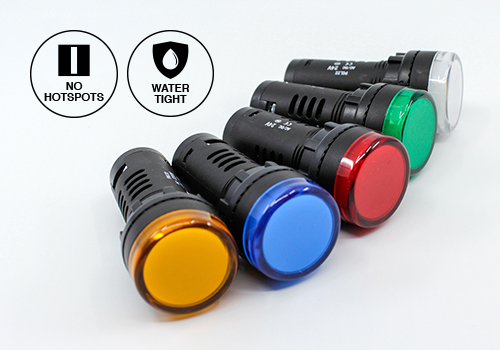
PCL22 Series
There’s no product line more perfect for keeping pizzas at the perfect temperature than VCC’s PCL22 Series. VCC recently launched the PCL22 Series, a 22mm pilot light solution that enhances visual communication even further with a large pilot light that offers uniform illumination. The PCL22 LEDs are simple to install, eliminate hot spots, and can be seen from a wide viewing angle, even at great distances.
The PCL22 Series was used for both red and green panel-mount indicators in 24V. These high-performance LEDs are watertight to IP65, helping make them the ideal pilot light solution for pizza warming cabinets, and include advanced light diffusion technology to eliminate hot spots. Single color options include red, green, white, blue, and yellow. A bi-color red/green option is also available for enhanced design versatility.
Omar Lara
Sr. Process Engineer, VCC
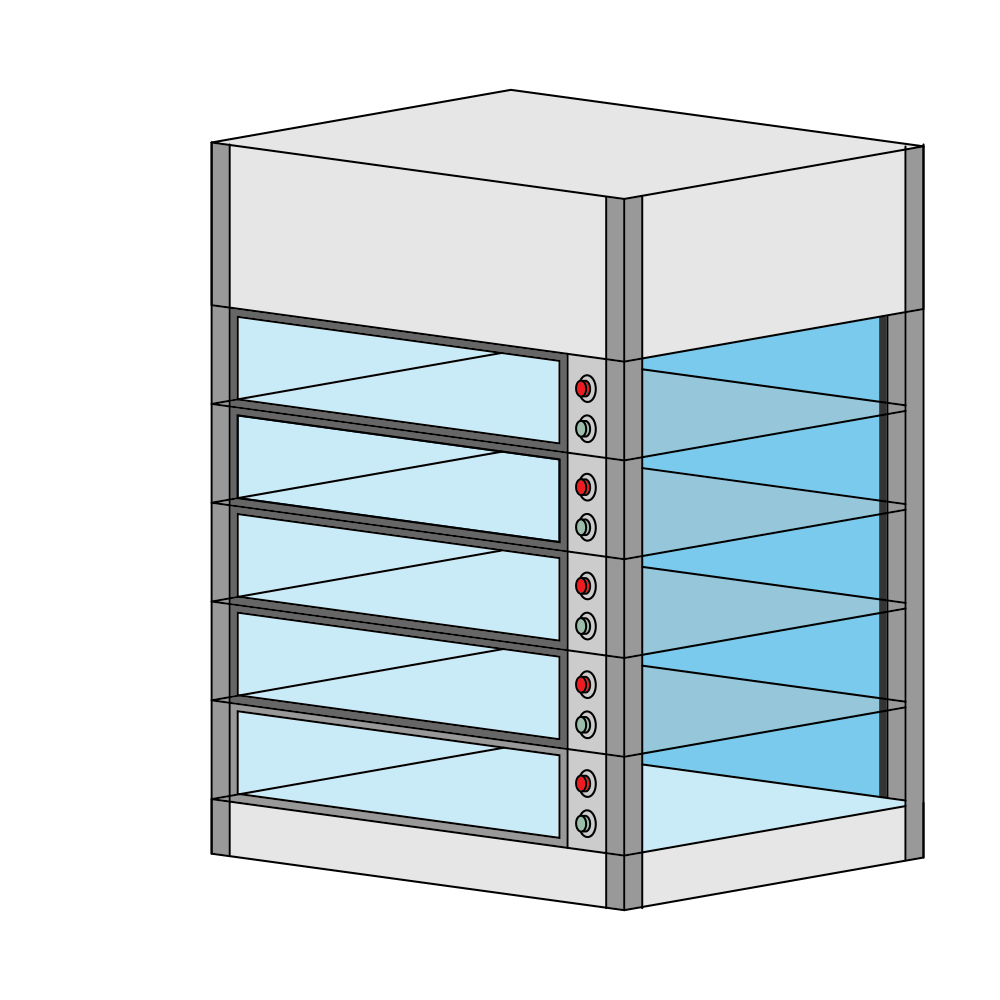
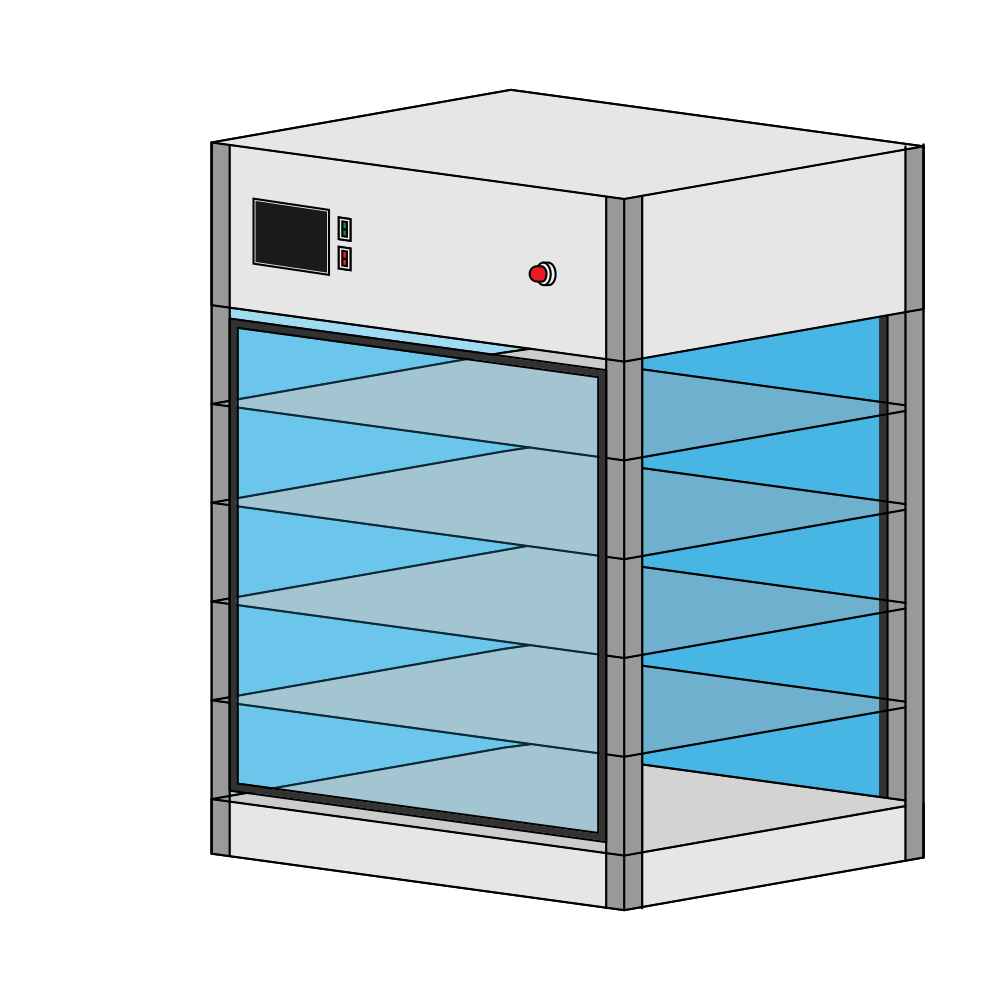
Results & Benefits
Through collaboration with the client, VCC’s design team combined neon and LEDs to provide a solution that ultimately delivers:
- Increased visibility for effective communication with users and customers
- Intuitive interface for hassle-free customer pick-up
- Consistently high-quality product delivery, which will lead to repeat business
- Higher order volume and increased efficiency without sacrificing quality
- Improved freshness of pizza due to constant temperature and humidity levels
- Reduced human error, which leads to a better customer experience
- Streamlined production time and costs due to using existing off-the-shelf products
- Supply chain simplification and reliability through nearshore manufacturing
Value-Added Services
By recommending standard components that met the client’s exact specifications, VCC helped the manufacturer save on production lead time and production costs. No prototyping was required to validate the design, meaning the pizza cabinet went to market faster.
Whether it’s pasta, pizza, or another beloved food group, VCC has the experience, quality and insights to ensure food safety and reliability are built into the design.
IoT is everywhere, but there’s still room for HMI improvement. VCC provides designs and components that enhance the user experience.