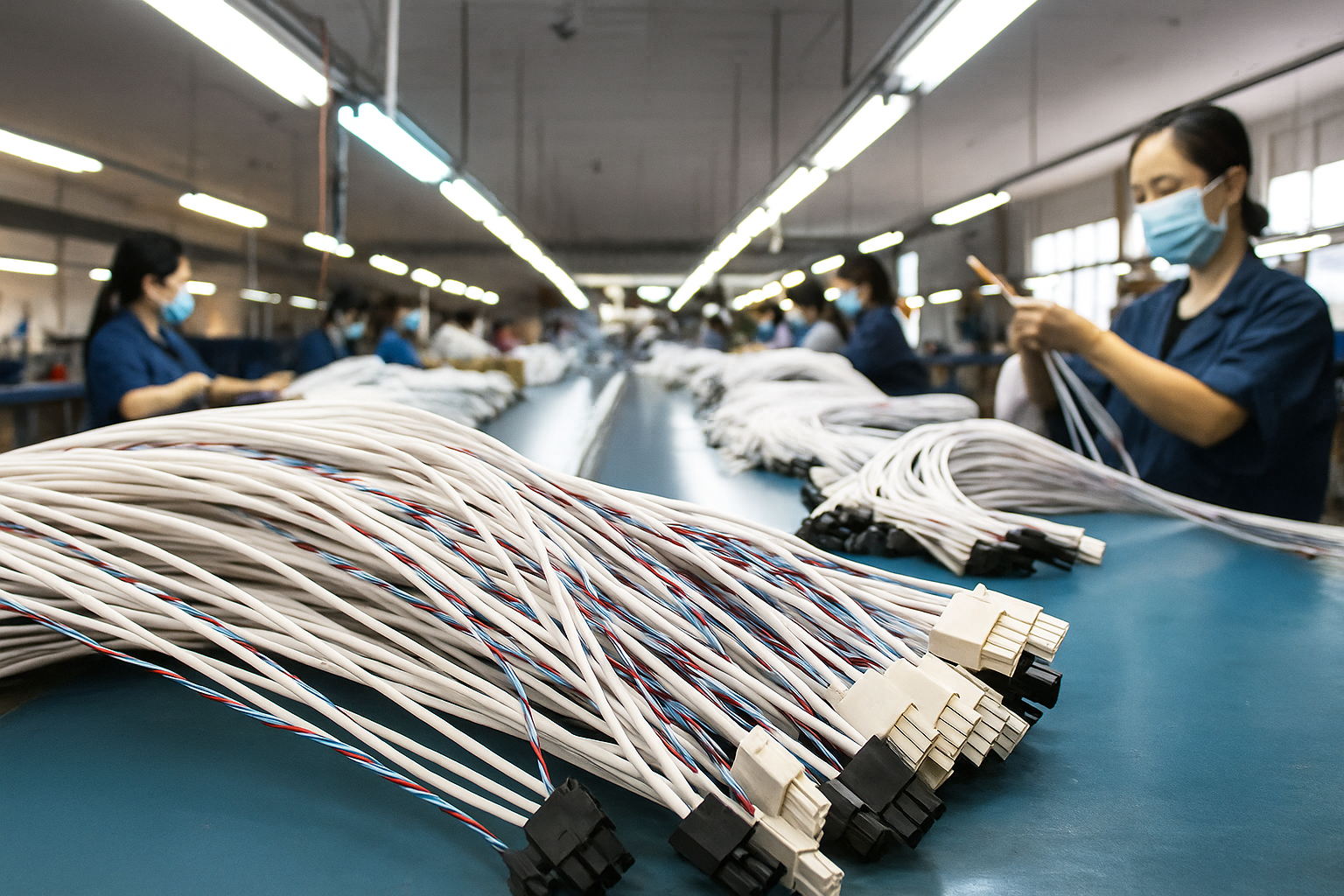
In the complex world of modern electronics, custom cable assemblies are more than just a collection of wires; they are critical pathways for power and data, carefully engineered to ensure seamless connectivity and reliability across various industries. The performance, life, and safety of any electrical system depend on the precise selection of conductor and insulation materials within its cable assemblies. This is especially true for applications in harsh environments where even small material compromises can lead to catastrophic failures.
At VCC, we understand that custom cable assemblies require in-depth manufacturing expertise and a comprehensive knowledge of cable types, components, and connectors. Our vertically integrated team works closely with OEMs and customers to select and integrate the right conductors, insulation, and protective sleeves, ensuring they meet exact design specifications and perform flawlessly under their intended operating conditions, with quick turnaround times.
The Foundation: Conductor Selection for Electrical Performance
The conductor is the metallic path for electrical energy, and its material, size, and construction determine the cable assembly’s current capacity, resistance, and signal quality.
Wire Gauge (AWG) and Ampacity
Wire gauge (AWG) defines a conductor’s ampacity—the maximum current it can carry without overheating. Thicker wires (lower AWG) have less resistance and carry more current. For example, a 10 AWG copper wire can handle 30-40 amps at 90°C, while a 24 AWG wire supports 4-5 amps. VCC engineers select the proper gauge based on voltage and current requirements to ensure safe and efficient power delivery.
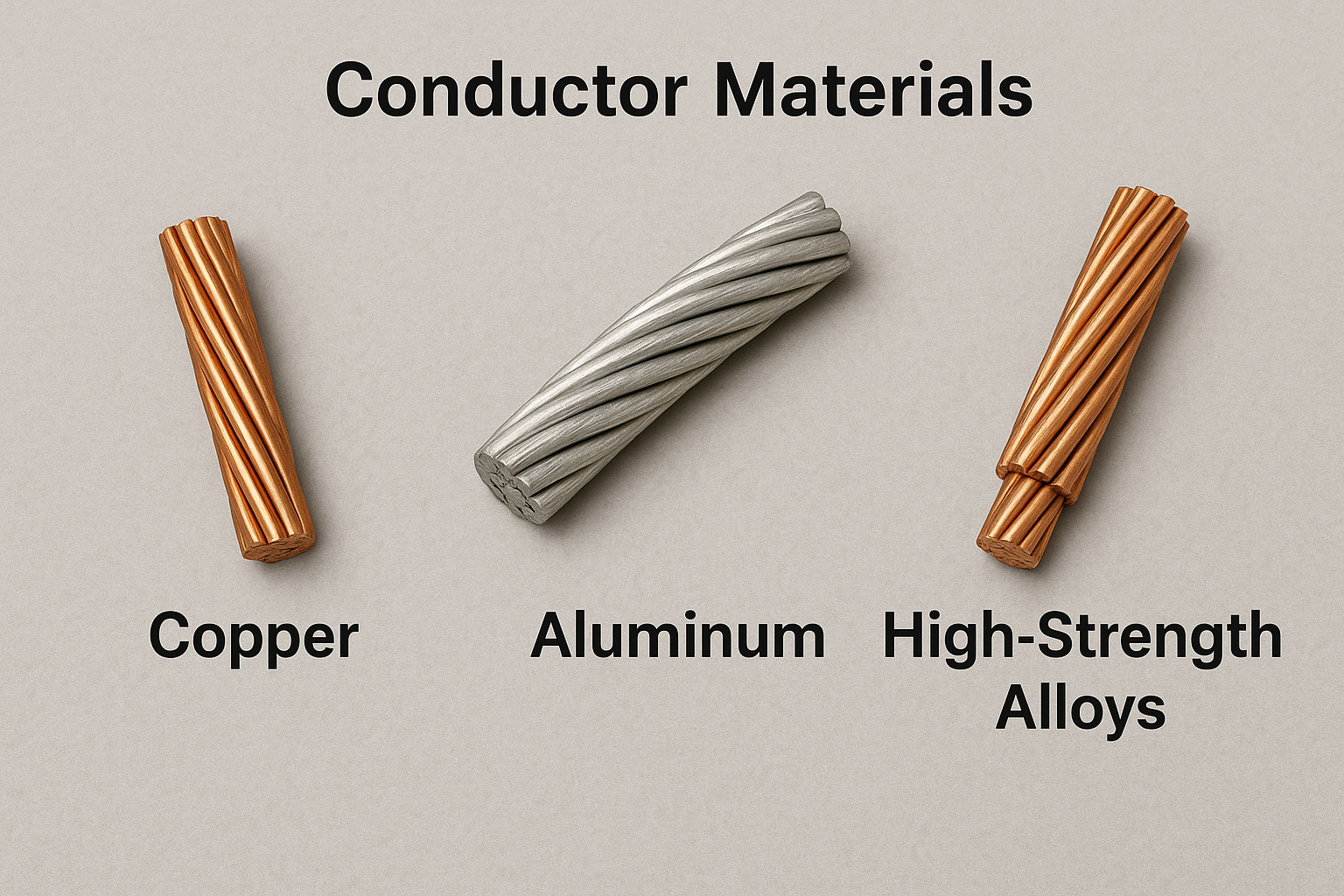
Conductor Materials
Common materials include:
● Copper: High conductivity, cost-effective, widely used.
● Aluminum: Lighter and cheaper but less conductive, used in low-voltage or weight-sensitive
applications.
● High-Strength Alloys: Such as copper-steel blends, used for added mechanical strength.
Plating Options
Platings improve performance:
● Tin: Prevents corrosion and eases termination.
● Silver: Enhances conductivity and temperature range, making it ideal for high-frequency applications.
● Nickel: Enhances corrosion resistance and high-temperature tolerance.
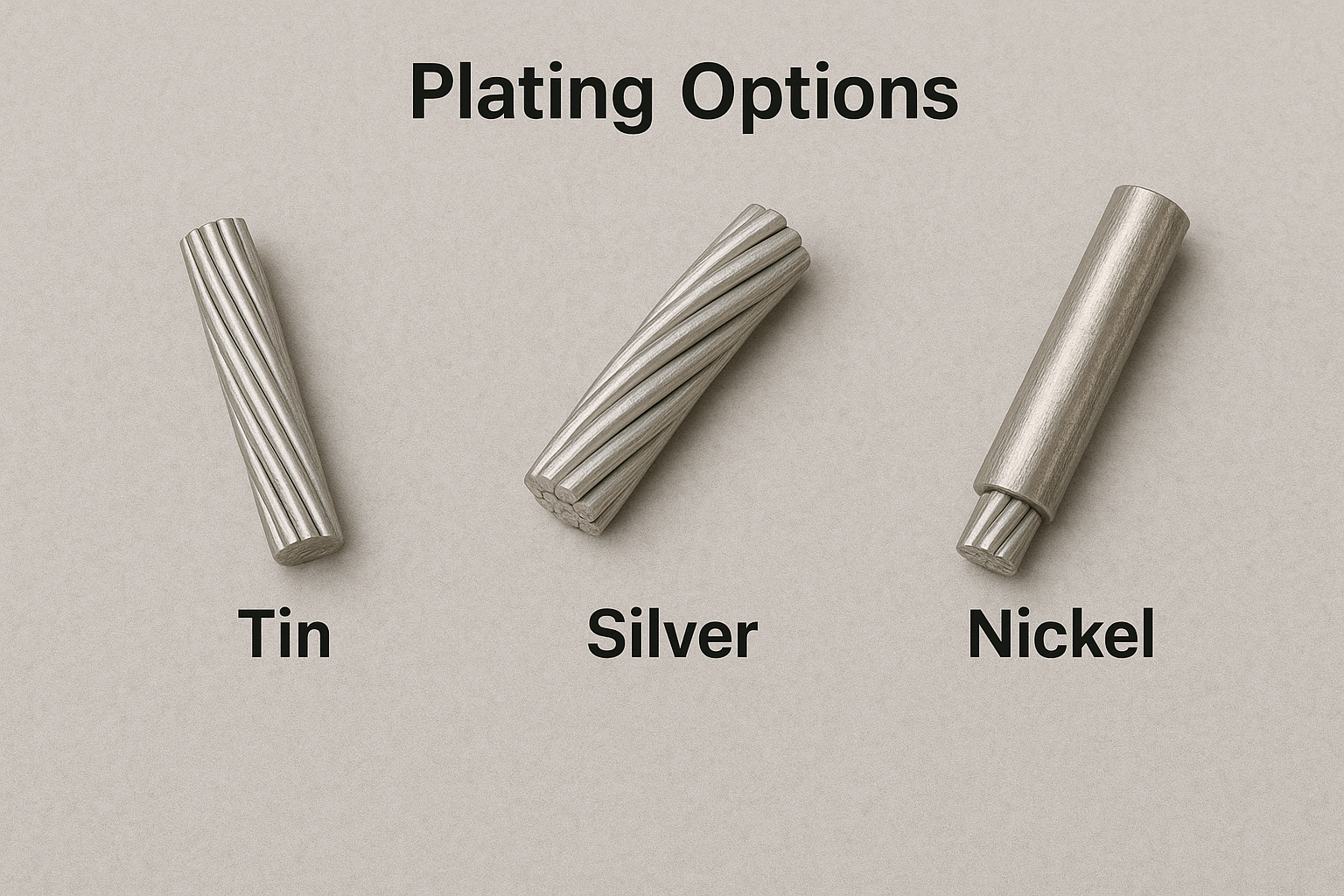
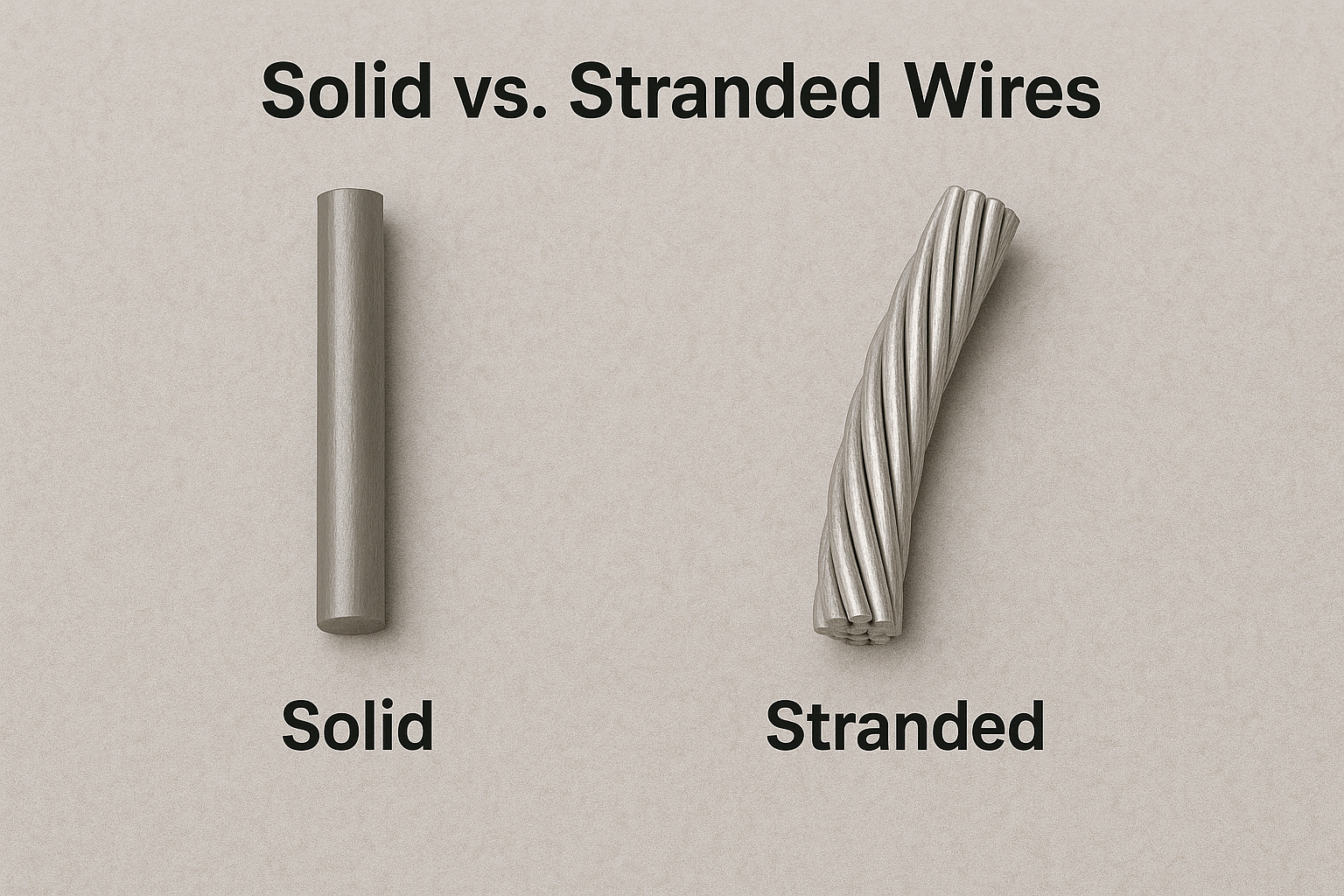
Solid vs. Stranded Wires
● Solid: Single core, less flexible, lower power loss, suited for high-speed or high-power needs.
● Stranded: Multiple thin wires twisted for flexibility, ideal for cables that move or connect frequently, though with slightly higher power loss.
The Outer Layer: Insulation and Jacket Material Selection
The insulation and outer jacket are essential for electrical isolation, signal integrity, and protecting conductors from environmental damage.
Insulation Materials
Insulation surrounds conductors to prevent shorts and maintain signal quality. Key properties include dielectric strength, dielectric constant, and a low dissipation factor, all of which contribute to efficient high-frequency performance.
Common insulation types:
● PVC: Flexible, flame- and moisture-resistant; suited for general indoor use, but with poor heat tolerance.
● PE/PP: Low dielectric constants for high-speed signals; PE is water resistant, and PP offers chemical resistance.
● Fluoroplastics (FEP, PFA, PTFE): High temperature and chemical resistance make them ideal for harsh environments, but they are also costly.
● PUR: Highly elastic and abrasion-resistant; suitable for frequent bending and industrial use.
● Silicone: High-temperature and weather-resistant; used in medical and aerospace applications.
● XLPE: Excellent insulation, heat, and chemical resistance; ideal for harsh conditions.
Jacket Materials
The jacket shields the cable from physical and chemical damage. Essential features include mechanical toughness, flexibility, environmental resistance, flame retardancy, and low-smoke, zero-halogen (LSZH) properties, all of which contribute to enhanced safety.
Materials like polyurethane offer superior abrasion resistance, while neoprene and thermoset CPE provide rugged environmental protection. PVC jackets are inherently flame retardant.
VCC's Expertise: Engineering Optimized Cable Assemblies
At VCC, our custom cable assembly and wire harnessing services are built on a foundation of deep engineering optimization and rigorous quality control. Our multidisciplinary team of experts knows that the optimal selection of conductor and insulation materials is not a one-size-fits-all solution; it’s a precise engineering challenge tailored to each unique application.
We work with OEMs from the initial design review, analyzing electrical, mechanical and environmental specifications. This proactive approach allows us to:
● Optimize for Performance: By carefully considering wire gauge, conductor material and insulation properties we ensure the cable assembly meets precise electrical requirements, including current capacity and signal integrity, even for high speed data transfer.
● Enhance Durability: We select materials and design constructions that withstand the specific environmental stressors of your application, whether it’s extreme temperatures, constant vibration, chemical exposure or moisture ingress. Our expertise extends to incorporating features like abrasion resistant jackets (e.g. heavy TPU or polyurethane coatings) and specialized conductors (e.g. multi-stranded copper cores) for enhanced resilience.
● Ensure Reliability: Our commitment to extensive testing and rigorous quality is paramount. We test electrical and mechanical, verifying that each cable assembly meets precise specifications before production. VCC maintains the highest standards of quality and precision from our North American IPC/WHMA-A-620-certified facility, so every assembly is built to last.
● Manufactured Under Strict International Certifications: UL (Underwriters Laboratories), CSA (Canadian Standards Association), MIL-Spec (Military Specifications), RoHS (Restriction of Hazardous Substances), REACH (Registration, Evaluation, Authorisation and Restriction of Chemicals), and VW-1 Flame Test.
By working with VCC you leverage our expertise to navigate the complexities of material selection, so your custom cable assemblies are not only cost effective but also deliver unparalleled electrical and environmental performance, getting your product to market faster.