In today’s fast-paced industrial world, efficiency is essential. For OEMs and systems engineers, reducing downtime and improving usability is critical—and much of that hinges on the Human-Machine Interface (HMI).
As Industry 4.0 accelerates, standard HMIs fall short. Custom solutions are becoming the norm, offering better functionality, longer lifespans, and smarter operator alignment in complex, regulated environments.
Generic HMIs can’t always account for the complexity of today’s equipment or the harsh environments of aerospace, transportation or heavy industry. Equipment reliability can be compromised if HMIs aren’t designed for the application environment, regulatory standards or daily workflow nuances that end-users face.
Beyond core functionality, pressure to comply with regulatory frameworks like IEC 60204-1 and ISO 13849-1 is intensifying. This intersection of regulatory compliance, ergonomic operator needs and efficiency goals demands expertly engineered custom HMI solutions.
VCC’s experience in the solution life cycle – from early discovery discussions to production build – allows teams to address industry-specific HMI needs. Custom HMI solutions may involve optimizing tactile feedback for gloved-hand usage common in oil & gas or using specialized optoelectronic components for improved visibility in medical or military devices. Let’s look at the key benefits:
1. Ergonomics and Usability: Poorly designed HMIs account for nearly $70 billion in annual losses due to operator error, misinterpretation, or fatigue. Custom HMI solutions eliminate these pain points by configuring control surfaces, indicator positions, and actuation feedback to match real-time user expectations and site conditions.
2. Environment-Readiness: Factors like chemical corrosion, humidity, UV exposure, and wide temperature brackets mean OEMs must choose the right materials and interfaces from polycarbonate windows to IP67-sealed buttons. For example, VCC has delivered push-button assemblies for offshore wind electric facilities that maintain tactile accuracy after 5 million actuations and full exposure to salt fog.
3. Intelligent Integration: Future-ready HMIs go beyond switches and buttons. They incorporate modular light pipes, illuminated switches, and advanced signaling devices that interact seamlessly with PLCs and IoT-enabled diagnostics. VCC’s custom indication arrays can port vital sensor and status feedback directly to operators, closing the communication gap and speeding up response.
4. Branding and Differentiation: In crowded B2B markets, having a unique look while ensuring maximum clarity gives you an edge. VCC’s in-house engineering and fabrication provide clients with options, including branding colors, engraved legend plates, and custom backlighting, to ensure one-of-a-kind panel designs that reinforce their market position.
Custom HMIs aren’t a luxury—they drive measurable ROI. One client saw a 16% boost in line efficiency after replacing unclear indicators with high-brightness LEDs and tactile controls.
Well-designed HMIs can reduce downtime by up to 33%, while also lowering service costs, easing compliance, and enabling quick tech upgrades.
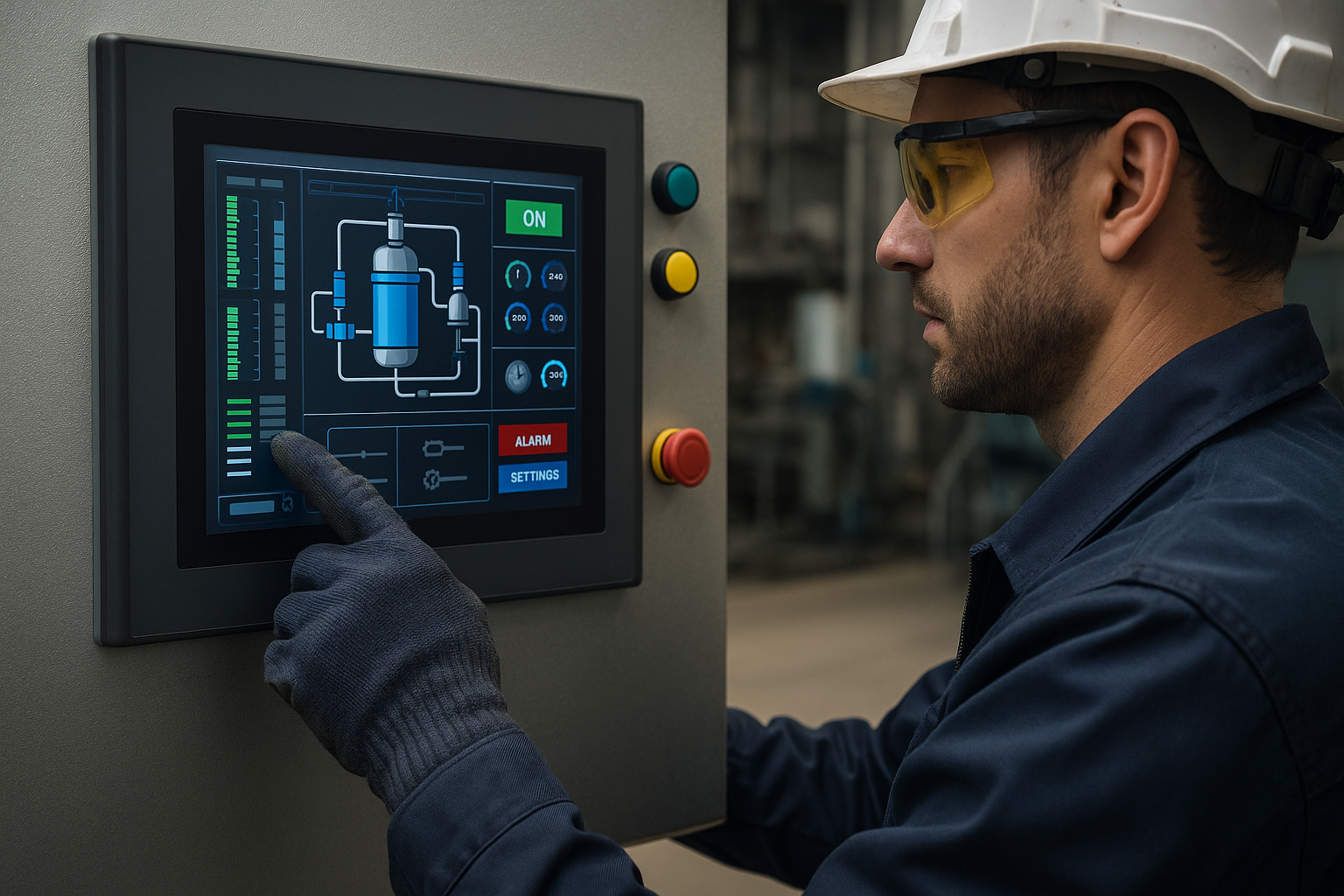
Generic interfaces often require costly retrofits. VCC’s agile approach—rapid prototyping, iterative feedback, and low-volume flexibility—speeds up delivery and reduces design changes, all while aligning engineering with production teams.
Whether it's programmable displays, adaptive lighting, or multilingual interfaces, VCC designs for now and what’s next.
Built for Compliance, Engineered to Last
From transit and automation to food processing and energy, every VCC HMI meets global standards like UL, CE, IEC, and DIN. Features include:
-
EMI/ESD protection
-
Thermal and optical tuning
-
Self-diagnostic capabilities
These ensure reliability through certifications, audits, and everyday operation.
Rail Retrofit:
In a vibration-heavy, gloved-operator environment, VCC designed oversized, sealed switches with domed lenses and CAN-bus integration—reducing input errors and improving safety.
Food Processing Line:
Facing strict washdowns and traceability needs, a client adopted VCC’s corrosion-resistant, sealed indicators—doubling interface lifespan in high-moisture settings.
Q1. How are custom HMIs different from standard ones?
They’re designed for specific environments, users, and functions—unlike generic interfaces that may fall short in real-world conditions.
Q2. Can VCC support both prototyping and production?
Yes. We handle everything from rapid prototyping to full-scale production.
Q3. Are VCC’s solutions compliant?
All products are designed to meet global regulatory standards, accompanied by comprehensive documentation for full traceability.
Q4. Which industries benefit the most?
Transportation, energy, automation, aerospace, medical, and food processing.
Q5. What’s the typical turnaround time?
Anywhere from a few weeks to several months, depending on complexity. We prioritize speed and clarity throughout.
Industrial leaders don’t just install interfaces—they design smarter systems. VCC bridges design intent with real-world performance through custom HMI solutions built for growth, reliability, and usability.